Stationary Units/ ES2000 Series Shredder
ES2000 Series Shredder
The Toughest Shredding Applications: “The Beast”
The ES2000 Series Shredder is made with a proprietary BCA hydraulic cluster system that allows for instant RPM change based on load requirements for MAX throughput. “The Beast” can be used as a primary or secondary reduction within your system. The ES2000 has several different add-on options to account for your specific needs. Shred just about any material imaginable, including tires waste, metals, and more.
“The Beast” is available in Hydraulic/Electric, Hydraulic/Diesel, and All Electric Models.
- 48″ to 72″ x 44″ cutting chambers
- 8″ 4140 Chromoly steel shafts
- BCA 6 keyed “no washout” shaft system
- 24″ diameter AR500 base alloy with hard-faced edge knives
- Cleaning fingers and dead-zones
- Proprietary hydraulic cluster drive system
- Variable displacement systems superior in high throughput applications
- Auto reverse protection/Overload protection
- Full PLC control for system integration
- Hydraulic or electric
- Touch screen programmable controls
- 24,000 to 32,000 lb unit made in the USA
- Dual cutting chambers available
- Up to 800HP rated
- BCA recirculation system
- Custom screens and magnets are available
- Custom BCA systems in 3D design
- Conveyors, hoppers, reclaim bins, etc.
- BCA patented TRIPLUS knives are available for SHRED-CHIP-SIZE in one pass
- System set-up and on-site training
- All electric ES2000 version available
- Semi, Supers, Automotive, & Light Duty Truck Tires
- Batteries
- Waste
- Paper, Plastics, & Composites
- C & D waste
- Ferrous & Nonferrous Metals
- Organics
- MSW
- Electronic Waste
- Ragger Tail
- More
Custom System Configuration Samples
Contact BCA Industries today for a free quote on the ES2000 shredder.
Analysis and Comparisons for other High Torque Shredders
The BCA Industries ES2000 “THE BEAST”
PROBLEM: The number one cause of complaint about shredder systems are the “catastrophic cost” failures and associated downtime.
SOLUTION: BCA shredder systems are designed from start to finish to minimize and eliminate the poor designs causing these problems from competitors’ shredders that were engineered 40 years ago and are the same today.
PROBLEM: Shredder companies use 4140 knives, traditional hard-face welding, or even just tool steel for their systems. Inferior knives increase your number one maintenance cost…knife rebuilds.
SOLUTION: BCA proprietary knives are a base military grade alloy at 56 RC and the newest “Super Edge” hard face weld bringing the cutting surface to 68 RC. This involves machining and welding using extraordinary methods pioneered by BCA to increase knife life by 50% and more but at the same costs. Longer knife life means profits for the owner.
PROBLEM: Expensive shaft washout and failure can be caused by undersized material, poor shaft design, and poor clamping nut design that can allow loosening of the stack during operation. Another “catastrophic failure”.
SOLUTION: Instead of 7” shafts BCA uses 8” Chromoly shafts for the ultimate in shaft life. Where others use the old HEX shaft design or a double-key round shaft BCA uses a 6-key design where the knife literally rides on the disposable keys and not directly on the shaft. This design although requiring more machining and precision eliminates shaft washout and simplifies knife changes. The key takes any abuse instead of the shaft again insuring no “catastrophic costs” in its maintenance.
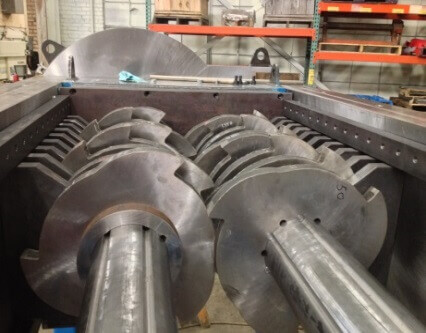
PROBLEM: Single RPM from other hydraulic shredder manufacturers never maximize throughput regardless of load. Most use just a single rotary piston pump.
SOLUTION: BCA utilizes a pressure-compensated variable displacement pump that allows the RPM to increase and decrease based on load maximizing throughput and efficiency. This new application of technology finally realizes a high torque shredder’s ultimate capability.
PROBLEM: Gearbox failure leaving the customer with an expensive repair and typically long part lead times leading to expensive downtime.
SOLUTION: The BCA redundant drive hydraulic system employs a simple gear design using 1-pitch gears for heavy-duty use rather than light-duty 4-pitch gears used by others.
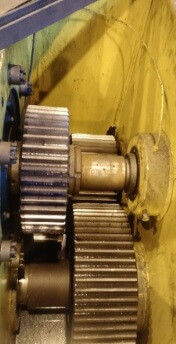
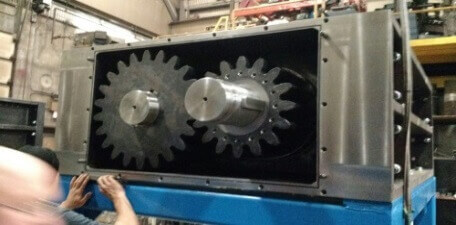
PROBLEM: Most shredder manufacturers when building Hydraulic power supplies use a single and very expensive Hydraulic pump and motor. The most typical used can cost $50k to $70k to replace and have lead times exceeding 12 weeks to get. That’s more downtime and catastrophic expense built into their designs.
SOLUTION: The BCA proprietary Redundant Cluster Drive System uses smaller redundant and less expensive American made hydraulic motors allowing you to keep running even when a part fails in the years ahead. In fact with 8 separate but matching motors that create the incredible torque specified, the 2000 series not only keeps running for you but keeps the part lead times to just a day or two for a small fraction of the typical costs.
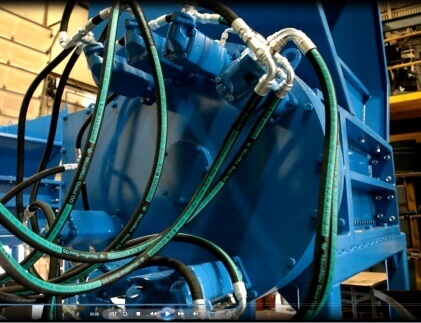
PROBLEM: Bearing failure due to contamination are common problems. Bearing seals and shaft armor simply are not enough to protect against the compression forces in a shredding chamber leading to “catastrophic costs” for the customer.
SOLUTION: All BCA shredders are designed with a double labyrinth-style drop zone and outboard bearings. This eliminates any direct path to the shaft bearings and allows compressed material a path to exit the shredder. This saves the customer the “catastrophic costs” of bearing and shaft replacement.
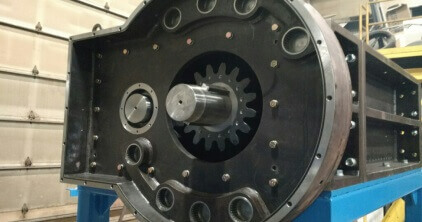
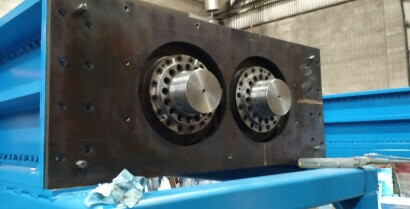